Improving usability with the tna robag former & unload assist
January 22, 2020
Across the packaging and processing industry, we continually look for ways to make operations simpler and more time efficient. Greater flexibility of products, that enhance performance and lend themselves to seamless operations are the most sought-after options by customers. Here is where product ergonomics can play a pivotal role, not just in enhancing performance but also reducing labour time and increasing uptime. With that in mind, tna developed the former unload assist configuration for its tna robag® series: an innovative solution aimed at improving access for operators.
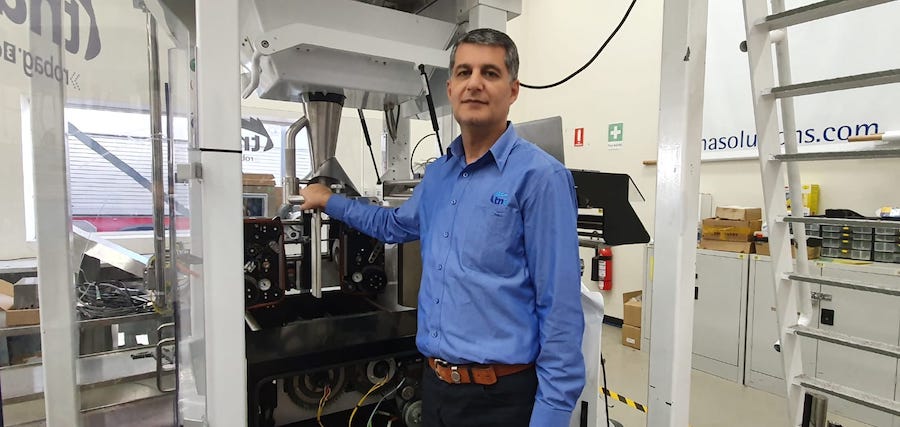
The challenge with formers
As a research and design engineer, I’m responsible for supporting sales engineers around the world. In this role, I’ve learnt that concerns regarding formers are commonplace, as any issue can cause substantial delays on the production line. An integral part of any packaging system, they allow products to be efficiently packaged – transforming flexible film into a tubular configuration, into which the product is then inserted. The film tube is then sealed horizontally and vertically to form a pillow bag. But during a production run, formers often need to be replaced to cater for changing pack sizes and/or types, as well as the regular servicing and maintenance that keep systems running smoothly.
Historically, changing out formers can pose a significant challenge for operators. They are typically located inside the packaging cabinet, where you must manually reach in, lift the former and remove it from its saddle. Understandably, this can be a time-consuming process as the former is not usually ergonomically positioned.
All systems go
To help operators, we adapted the popular tna robag® series to include an improved ergonomic design. The former unload assist features an innovative pivot arm assembly, which facilitates the unloading and replacing of the former quickly and easily. An original and patented design, the arm swings out from a running position on the support assembly to a 90-degree angle. This means you can place both hands on the former and lift directly without leaning and twisting the torso, thereby reducing the risk of injury; a feature that has been appreciated by operators.
What does all this mean?
The addition of the former unload assist means operators have much greater flexibility when it comes to switching between pack sizes and types. The ability to change out formers using side access, rather than the traditional front access, not only improves product changeover times, but also requires minimal manual effort. From a manufacturer’s point of view, being able to make quicker former changes increases production uptime and improve overall plant performance. And who doesn’t want that?
For further information about our robag® series, visit: http://www.tnasolutions.com/solutions/packaging-solutions/