Increasing productivity in food processing & packaging plants: 3 ways effective aftermarket service can help
April 22, 2020
In today’s commercial landscape, food manufacturers are under increasing pressure to improve the efficiency of their processes to meet evolving market demand and uphold operational profitability. Beyond installation, the challenge for operators lies in successfully maintaining and repairing equipment as quickly as possible to keep production downtime to a minimum and ensure high productivity levels. While providing effective training to new and existing staff on an ongoing basis is vital to safeguard the efficiency of packaging operations, it often falls under the radar in a busy production environment.
Here, we discuss the top three ways an end-to-end solutions provider with a broad aftermarket service portfolio can support plant managers in increasing productivity:
1. On-hand technical expertise
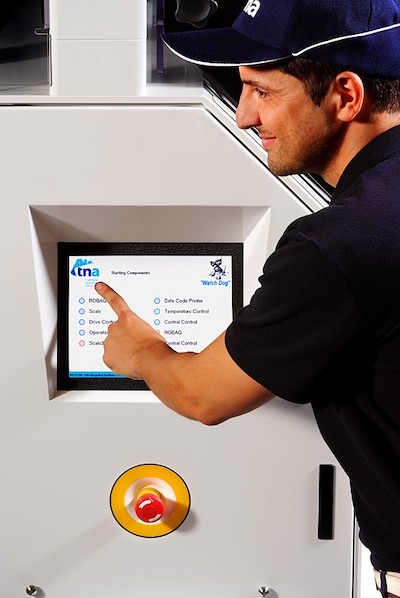
Regular servicing is crucial to ensure equipment runs smoothly and efficiently over its lifespan. Having said that, a food production plant often incorporates a wide range of equipment, while systems are becoming increasingly sophisticated. This can present a complex challenge for operators, since every machine has its own specific features. An in-depth knowledge of specifications is therefore required to perform maintenance tasks effectively.
A quality aftermarket service provider can provide the technical know-how required to do just that. Through their intricate understanding of each and every piece of hardware, software or electrical equipment, they can meet customers’ holistic requirements and integration protocol. From remote assistance to on-site visits, ongoing technical management and support is a key consideration when it comes to ensuring the productivity of your plant.
2. Availability of spare parts
Do you have spare parts at hand if your packaging system goes down? In the demand-driven world of food manufacturing, spare parts are vital assets for maintaining productivity. Having spare parts readily available, means that manufacturers can carry out repairs and replacements as quickly as possible to avoid lengthy shutdowns and meet production goals.
Alongside technical expertise, a high quality aftermarket service means that operators can readily access genuine high-, medium- and low-wear spare parts whenever they need them, no matter the location. While standard parts are often readily available, it’s important to note that the replacement of customised parts can often result in longer lead times. However, a dedicated partner can support manufacturers in finding an alternative solution that keeps equipment up and running until the necessary part arrives.

Flexible training solutions
Among the factors that contribute to the overall efficiency of a food production plant, a fully trained workforce is top of the list. To make the most of the equipment’s potential and ensure processes run smoothly once an installation is complete, operating staff and engineers must understand the capabilities and characteristics of the systems, inside-out.
A first-class aftermarket solution incorporates a wide range of training solutions to cover every technical aspect of the machine(s) that might need attention. Examples include product-specific operator training, covering safety, installation, trouble-shooting guidelines, cleaning requirements, as well as maintenance training. Simultaneously, training modules should be tailored to the customers’ bespoke needs and delivered with onsite, offsite or online – i.e. to cater for different job roles, skill levels, or team member’s location in different geographies etc.
A partner for life
tna’s commitment to quality and innovation extends to the life of our customers’ equipment with our my-tna 360 customer care programme. Through this market-leading service, we’re able to offer ongoing and continuous support to our customers – keeping them up-to-date with the latest product updates, new solutions upgrades and breakthrough innovations.
For more information on tna’s aftermarket endeavours, connect with our team here: http://www.tnasolutions.com/support/tna-helpdesk/