Driving sustainable growth with innovative packaging technology
December 11, 2019
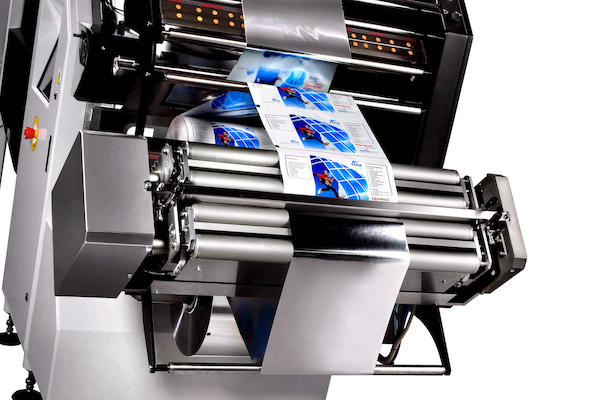
With topics such as climate change owning the headlines worldwide, sustainability is unlikely to be crossed off the agenda any time soon. Promoting sustainable food production, including packaging, has therefore become a top priority for manufacturers. Here, we put the spotlight on packaging and discuss how the latest vertical form fill and seal (VFFS) technology can help producers create a more sustainable food industry.
Promoting sustainability in food packaging
Fuelling sustainable growth, VFFS systems have been designed to increase productivity without investing more resources, such as time, energy and manpower, or introducing additional machines. This technology enables producers to streamline their packaging process with a single piece of equipment and deliver optimised packaging speeds and yield to achieve maximum productivity and energy savings. VFFS technology can also support producers in reducing product waste to levels as low as 0.5%, elevating the brand and/or products’ sustainability credentials to the next level.
VFFS equipment typically requires less plant space than horizontal packaging systems. Its vertical layout results in a small footprint, which frees up floor space, but also means manufacturers can consider multiple packaging lines in a limited space. This allows them to increase packaging yield as demand grows, without expanding plants. The vertical layout also ensures staff can access machines easily when completing services or repairs, avoiding operational downtime.
tna robag®: a sustainable design
A fully integrated VFFS solution, tna’s robag® technology can add value to brands and products by improving both the sustainability and economic efficiency of food manufactureres’ packaging lines. Key features include:
- Single serration jaws: Specifically developed for tna’s robag® technology, they help create a pillow-like bag with a smaller seal area to either increase bag volume while maintaining the same bag length or reduce film usage with the same volume. Due to their minimised profile, these systems require less jaw heat (and therefore less energy), while achieving a faster seal time and improving end product quality.
- tna robag® auto-splice: Improves packaging speeds and yield by automatically splicing film — joining the start of a new pre-prepared roll of film to the end of an expiring, without disrupting the packaging process or causing operational downtime.
- Stripper tube closures & product-in-seal-detection software (PISD): Part of the tna robag® jaw system, the stripper tube closures guarantee a fast and accurate product transfer with minimum waste by ensuring no products are lost by falling through the seal area. PISD software also monitors products in the seal and jaw area and immediately alerts the operator if the seal integrity is compromised, so that bags can be quickly removed from the line for inspection. This ensures that each bag meets the highest quality standards and waste is kept to an absolute minimum.
- Power saver software: With features such as ‘stand by time’, it can significantly lower a plant’s energy usage and carbon footprint.
Looking ahead
By implementing market-leading VFFS technology, such as the tna robag®, manufacturers can achieve maximum productivity with minimum waste and footprint, increasing the economic efficiency and sustainability credentials of their brand and its products. Aside from enabling them to limit the detrimental impact their operations have on the environment, it equally creates a stronger appeal for today’s discerning consumers and contributes to a more sustainable food economy.