Top 3 considerations for future-proofing your cereal success
July 7, 2020
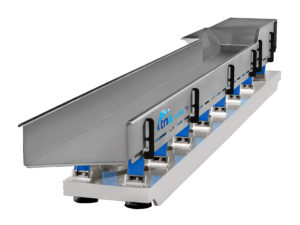
It may come as no surprise that the coronavirus pandemic has set in motion a series of unprecedented events affecting the entire food and beverage industry. With almost an overnight shift in consumer buying behaviour, there has been a surge in demand for eat-at-home products with a long shelf life, such as breakfast cereals and snack bars. What’s more, with the Food and Agriculture Organisation’s prediction that wheat production will reach near-record levels later this year, the outlook is positive still.
That said, the real impact of the pandemic is not yet known – will demand simply return to “normal” levels? Or should we expect a new normal (still to be defined) in the post COVID-19 era? As such, it’s more important than ever before that cereal producers futureproof their production lines – to not only be able to cater to changing consumer preferences, but also cope with sudden fluctuations in demand. Here, we discuss our top 3 considerations to ensure your cereal line is fit for future requirements.
- Flexible operations
Brand owners need to be able to continuously adapt their processing lines when looking to meet new and evolving market conditions. A flexible approach to cereal production is therefore vital if recent months are anything to go by. The incorporation of modular systems, for instance, means production output can be easily modified or extended with additional units, if required.Where multiple products must be processed on a single line, the ability to offer fast changeover times and minimal clean down requirements is essential when it comes to maximising efficiencies. Similarly, the freedom to adapt and exercise precise recipe control is also an important factor in ensuring flexible and efficient operating practices. For example, systems which allow for programme parameters to be stored as recipes and easily adjusted at the touch of a button offer processors the ultimate production flexibility. - Complete automation
The incorporation of modern automation technology is arguably essential for future-proofing operations. Offering several advantages, it can help manufacturers target inefficiencies, secure food safety via traceability, create a more efficient workforce, reduce waste and control energy costs – to name a few. So, in a climate like the current one, where every penny counts, such technology could be key to remaining profitable.Perhaps more importantly, however, it can support brand owners in tackling the pace of market change, enabling a more agile response to fluctuations in demand, while maintaining the operational integrity of their plants. Over recent months, we’ve witnessed several manufacturers having to do exactly that – the ability to quickly reconfigure a production line therefore cannot be undervalued. - A turnkey approach
The concept of ‘turnkey’ means different things to different people. For some, it’s about offering systems, services or solutions that merely require you to ‘turn’ the key and they are ready to go with little-to-no configuration. This can be important when looking to upscale output in a short amount of time. In reality, however, ‘plug and play’ systems are few and far between. In fact, turnkey equipment typically requires significant customisation, so that it’s operational the second you turn the key. For many therefore, a turnkey approach incorporates design, manufacturing, commissioning and installation of equipment, as well as after-service technical support and user training.For many manufacturers, selecting a turnkey solutions provider for all their cereal production needs is a hassle-free way to ensure current and future manufacturing success. From analysing business needs and anticipating future requirements, to designing the technology, setting up the controls systems and training staff, every detail has been taken care of, no matter how small. In doing so, this helps to ensure their business is ready for anything.
A cereal-ously good choice
Regardless of the difficulties businesses may or may not be facing during these uncertain times, it’s important to be able to ensure business continuity for the long-term. Through its complete line of high-performance, flexible and reliable cereals processing and packaging solutions, tna aims to do just that. More than just a solutions provider, it also provides ongoing support and consultancy to ensure your installation delivers the highest return on investment, while also meeting your requirements for years to come.
You can learn more about our cereals capabilities here or contact us to discuss your specific requirements.