Give your products the gentle care they deserve with our complete range of industrial belt conveyor and vibratory conveyor systems. Whether for mixing, seasoning, sortation, coating, transporting or blending, our innovative solutions ensure your products remain exactly as you intended.
Our automated conveyor systems offer a smaller plant footprint than other solutions on the market today. Distribution solutions from TNA also have fewer moving parts to ensure lower maintenance requirements, quick and easy cleaning, and higher energy savings.
advanced food conveyor belt and distribution solutions
Our state-of-the-art food conveyor belt and distribution solutions offer even the busiest production lines efficiency and accuracy in food processing and packaging.
Our range of conveyor systems and distribution solutions includes:
tna roflo® VM 3
Our tna roflo® VM 3 is a conveyor system that uses vibratory motion technology to quickly and evenly distribute products without compromising on handling. Its patented design offers in-line storage and a variety of pan options to suit even the most niche production needs.
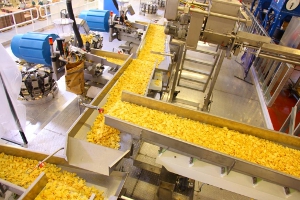
tna roflo® HM 3
Our tna roflo® HM 3 is a conveyor system that uses horizontal motion distribution that outperforms other industrial conveyor systems. Its patented gateless design and gentle sweeping motion drive efficiencies while reducing product breakage and seasoning loss. Further, the tna roflo® HM 3 offers easy cleaning and minimal seasoning build-up thanks to its quick-release pans. For products that are heavily coated, the tna roflo® HM 3 is an optimal solution.
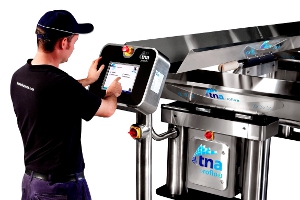
tna roflo® VMCS 3
Our tna roflo® VMCS 3 is a conveyor system that uses vibratory motion to size potato and other root vegetable chips. The tna roflo® VMCS 3 conveyor solution drives chip packaging efficiencies through automated chip sizing. This high-speed chip sizer features a cascading chip-sizing screen that helps get the right product into the right bag while reducing breakages. The tna roflo® VMCS 3 is not limited to potato chips either — it can size and sort chips from other root vegetables and fruit chips too.
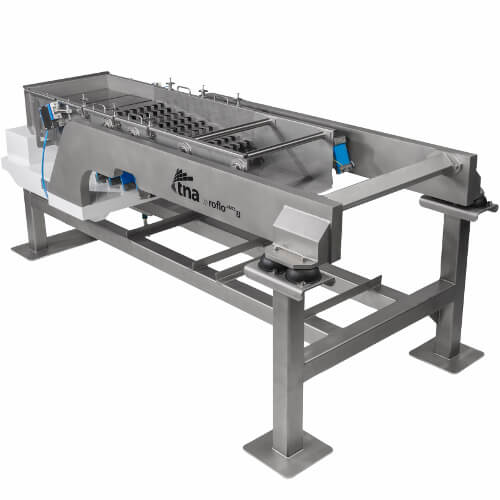
tna roflo® VMBS 3
Our tna roflo® VMBS 3 is a state-of-the-art vibratory motion blending system that accurately measures each individual ingredient. Speed, vertical conveyor motion and mass flow technology combine to regulate the distribution of both dry and wet ingredients, ensuring a perfectly proportioned mix every time. With fewer moving parts, less maintenance and energy are required.
Our modular design options make integration simple in virtually any plant, and the stainless-steel finishes help enhance food safety and ease the cleaning process to optimise uptime.
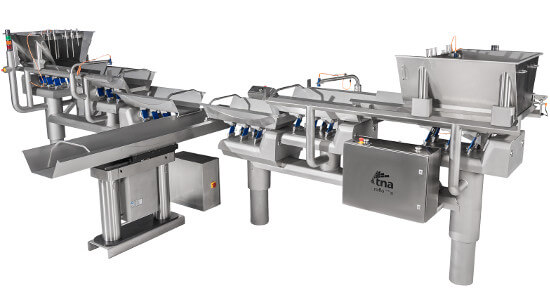
achieve your production goals with a host of conveyor and distribution features
For warehouse manufacturing companies in the food industry, conveyor solutions provide a fast, efficient and accurate means of packaging and processing your goods. Through expert design and automation, our conveyor systems help increase manufacturing throughput while freeing up your teams to focus on more value-added tasks.
Custom conveyor systems can deliver significant benefits to your food packaging production line operation, including:
- Lower labour costs
- Higher production rates and throughput
- Better quality control
- Improved compliance
- Enhanced worker safety
- Reduced risk of human error